James Bennett1, Karina Gonzalez2, Jürgen Gruber3, Günther Mayr3, Jonathan Glinz3, Johann Kastner3, Tobias Hötzer4, Balthasar Fischer4, Sascha Senck3
1 Hawkeye Spectral Imaging LLC, Tucson, Arizona, USA
2 Peak Technologies GmbH, Technologiepark Str. 6, 4615 Holzhausen, Austria
3 University of Applied Sciences Upper Austria, Stelzhamerstraße 23, 4600 Wels, Austria
4 XARION Laser Acoustics, Ghegastraße 3, 1030 Wien, Austria
Abstract
Composite Overwrapped Pressure Vessels (COPV) consist of an internal aluminum liner and a shell consisting of carbon-fiber reinforced polymer (CFRP). They are used in motor sports (smaller diameters up to approx. 100 mm) and in aerospace (larger diameters up to approx. 500 mm). COPVs have high strength and low weight, but internal defects like internal pores and debonds between the liner and the shell can lead to premature, fatal mechanical failure. Since the COPV diameter, especially in larger versions, limits the resolution of X-ray microcomputed tomography (XCT), additional non-destructive testing (NDT) approaches are neccessary. In addition to XCT, we analyse a 1200 cc COPV using air-coupled ultrasound testing (UT), laser ultrasonic technique (LUT), infrared thermography (IRT), and digital shearography (DS). Resulting image data is qualitatively analysed in order to compare the performance of the respective NDT technique in detecting the internal debonding between metallic liner and composite shell.
Keywords: COPV, delamination, ultrasound, thermography, shearography, microcomputed tomography
1 Introduction
The analysed sample is represented by a composite overwrapped pressure vessel (COPV) featuring an inner aluminium liner and a carbon fiber composite shell. COPVs are used in aerospace applications, e.g. for storage of pressurized gasses, due to the ratio between high-strength and low weight [1]. The 1200 cc COPV was manufactured in the following steps: 1) CNC machining of endcaps out of Al rods, 2) welding process to combine the endcaps (electron beam welding), 3) liner surface treatment, 4) CFRP filament winding, 5) curing in autoclave, and 6) autofrettage. The welded aluminium liner is enclosed by a seamless outer shell with elliptically curved end pieces and a cylindrical mid-section. The air bottle shows a cylinder opening with internal thread. The carbon fiber layers are wound in an orderly fashion on a spreader layer, which is optimally designed on the surface of the aluminium inner liner. The aluminium liner is treated by a “self-tensioning” approach during the manufacturing process. The longitudinally and spirally wound fiber layers are alternating around the main body part of the internal liner. In this process, the carbon fiber layers are wound in a central longitudinal direction and spirally around the end portions. The composite air bottle in the present design meets the required stress distribution and ensures that the composite part can withstand the maximum burst pressure using the least amount of fibers. The composite gas cylinder thereby shows the advantages of permanent air tightness and optimum safety performance.
The NDT of COPV is challenging since the aluminum liner and the CFRP shell have different acoustic and thermal properties [1]. This contrast can make it difficult for NDT techniques to distinguish between an actual defect like debonding or delamination and the natural boundary between the two materials [2]. The curvatures and varying thicknesses in COPVs may introduce additional artifacts in the respective NDT techniques, making it hard to accurately locate a debond. Furthermore, in techniques like ultrasound testing, the anisotropic nature of CFRP can lead to signal attenuation or scattering, reducing the method's effectiveness in detecting flaws at the interface. Finally, the location of the debond in the multi-layer structure can also affect detectability. Finally, deeply located delaminations are hard to detect using surface-level NDT methods like infrared thermography or shearography.
2 Materials and methods
The working pressure of the used bottle type (see Fig. 2) is 350 bar, while the proof pressure is 525 bar. The minimal failure pressure is defined at a threshold of 700 bar. To introduce defects, the COPV was subjected to dynamic pressure cycle tests from 30 to 350 bars. The failure of the bottle in this contribution occurred after 1000 cycles. The central, cylindrical COPV part of the part was analyzed using different NDT methods including XCT, UT, LUT, IRT, and DS. The detailed NDT protocol for the respective technique and results for all the used NDT approaches will be presented in the conference paper. The following paragraphs focus on the results of the IRT and DS results.
3 Results and discussion
The different regions of the COPV were scanned using IRT in reflection mode. Here, the excitation and IR camera are on the same side. For optical excitation, two flash lamps with 6 kJ electrical energy each were arranged in such a way that homogeneous illumination is ensured. The temperature field at the surface is recorded with a 200 Hz sampling rate. The measurement window was set to 640x512 px or 640x1028 px respectively. The measurement duration was set to 150 seconds. For IRT testing, the pressure vessel was divided into 6 segments, each with 5 viewing directions (end caps, side, transition areas in Figure 1). The component was aligned in the direction of the camera for each viewing angle and rotated segment by segment. IRT phase contrast images were calculated in the DisplayImg 6.2.5.4. The evaluation was performed with a focus on deviations in the individual resulting images. In Fig. 1, the result images for all 6 sections are shown. The red ROI indicates areas with defects in the CFRP skin.
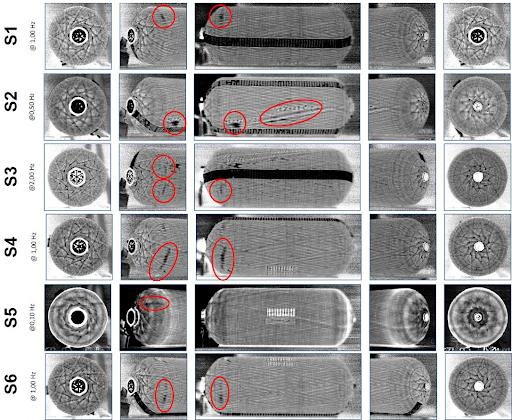
Due to the design, a classic pulse-shaped excitation for a transmission measurement was not possible. In order to realize an excitation from the inside of the pressure vessel, it was filled with warm water as quickly as possible. For this purpose, a funnel was glued to the connection piece. The vessel was measured in upright position. In Figure 2 the results of the IRT with hot water excitation are shown for the section S2. In the resulting images, it is very clear that there is a larger disbond. The warm water excitation allows a defect detection with a very good signal to noise ratio. For the digital shearography (DS) measurements, the pressure vessel was sprayed with a washable developer spray to obtain a white diffuse reflective surface. A commercial hot air dryer (Rapid Digit2000) was used to thermally excite the COPV. It was heated and the measurement was performed during the cooling process. Figure 2 shows a comparison of Active Thermography and Digital Shearography in the detection of a disbond in the COPV. It can be seen from this that with both methods the defect can be found unambiguously. Especially the thermography with a hot water excitation shows very good contrasts in the temperature image.
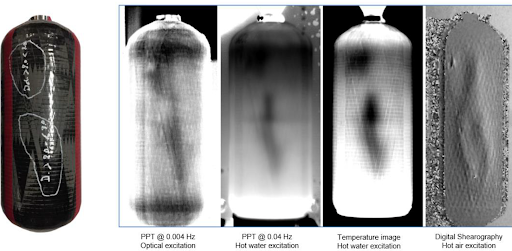
The first results using active thermography and digital shearography show clear indications of the extensive debond in the analysed COPV that was initially scanned by XCT. Since COPVs show a combination of small wall thicknesses, of both the inner liner and the external CFRP shell, XCT scanning resolution is low. In addition, a 100% using XCT may not be feasible for a given production line. Hence, alternative NDT methods have to be analysed in order to compare the performance in defect detectability, e.g. of debonds between liner and shell. In the complete conference proceedings paper, the results of XCT and UT analyses will be included together with a detailed description of the scanning protocols.
Acknowledgements
This work was supported by the project “SpaceNDT” in the course of ASAP14 (FFG) – financed by the BMVIT [FFG grant number 866013].
References
[1] Pat B. McLaughlan, Scott C. Forth, Lorie R. Grimes-Ledesma (2011). Composite Overwrapped Pressure Vessels, A Primer. NASA/SP–2011–573. National Aeronautics and Space Administration.
[2] David McColskey, Marvin Hamstad, Regor Saulsberry, Jess Waller (2015). NDE Methods for Certification and Production/Performance Monitoring of Composite Tanks. NIST report: 10.13140/RG.2.1.1726.9282